
To add a fan component to your SOLIDWORKS Flow Simulation project, first make sure the “Fans” folder shows up in your project tree. Rather, they use fan curve data provided by the manufacturer to create an output volume or mass flow rate based on the pressure difference between the inlet and outlet faces of the fan. Fan components do not attempt to physically model spinning fan blades. This blog will focus on the simpler and easier way to model the effect of a fan on fluid flow, using a “Fan” component in the flow simulation project tree. It is not recommended for the novice user or someone who is simply trying to simulate the effect of a supplied fan component that moves air (typically for cooling or ventilation purposes) in a flow application. This type of analysis is recommended for fan manufacturers who are trying to simulate the effect of changes to the fan geometry on the performance of the fan or pump manufacturers aiming to accurately calculate hydraulic head. This is a transient analysis and consumes a considerable amount of computational resource, typically resulting in exceedingly long solution times.
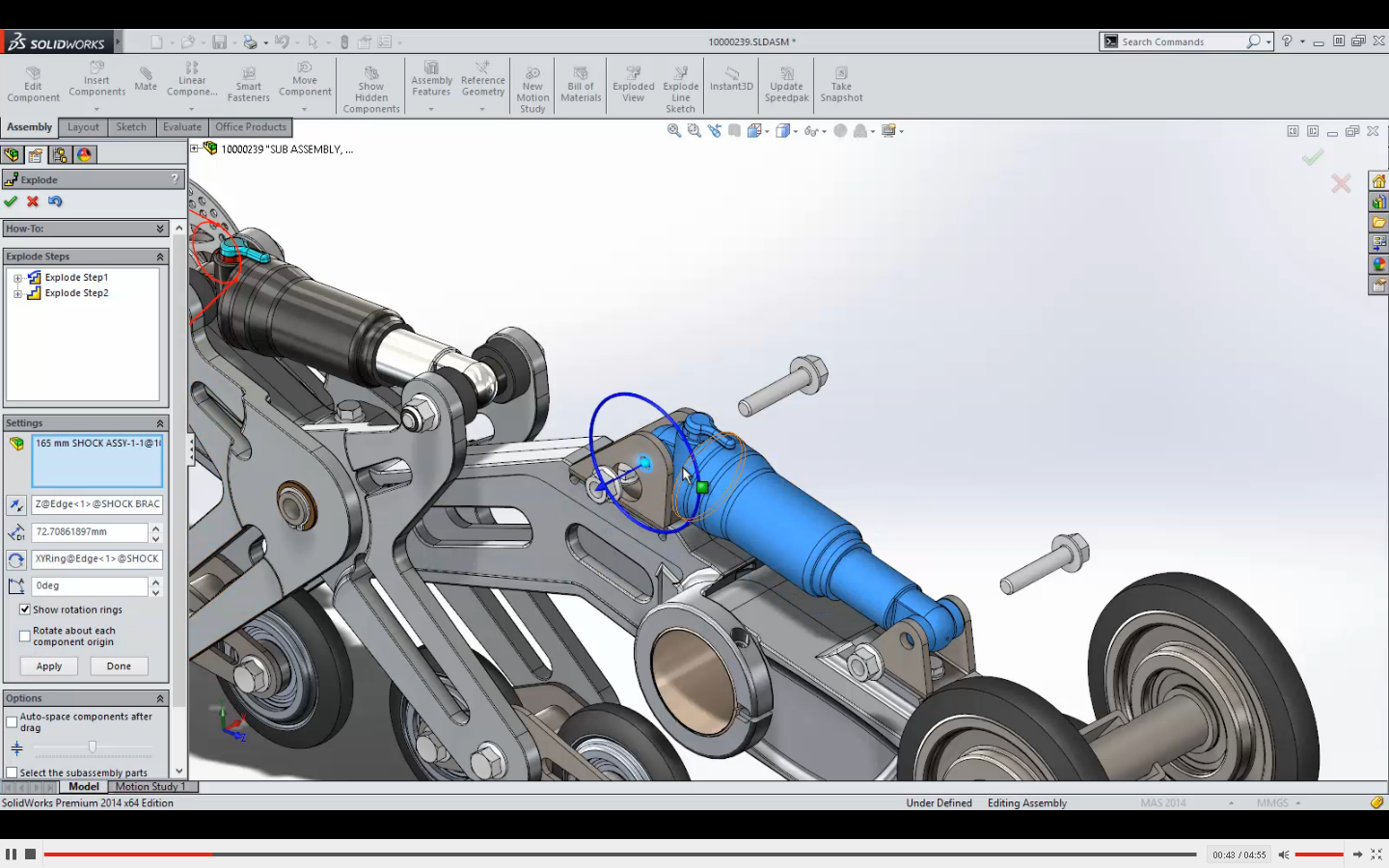
In this type of analysis, the mesh moves from one time-step to the next.
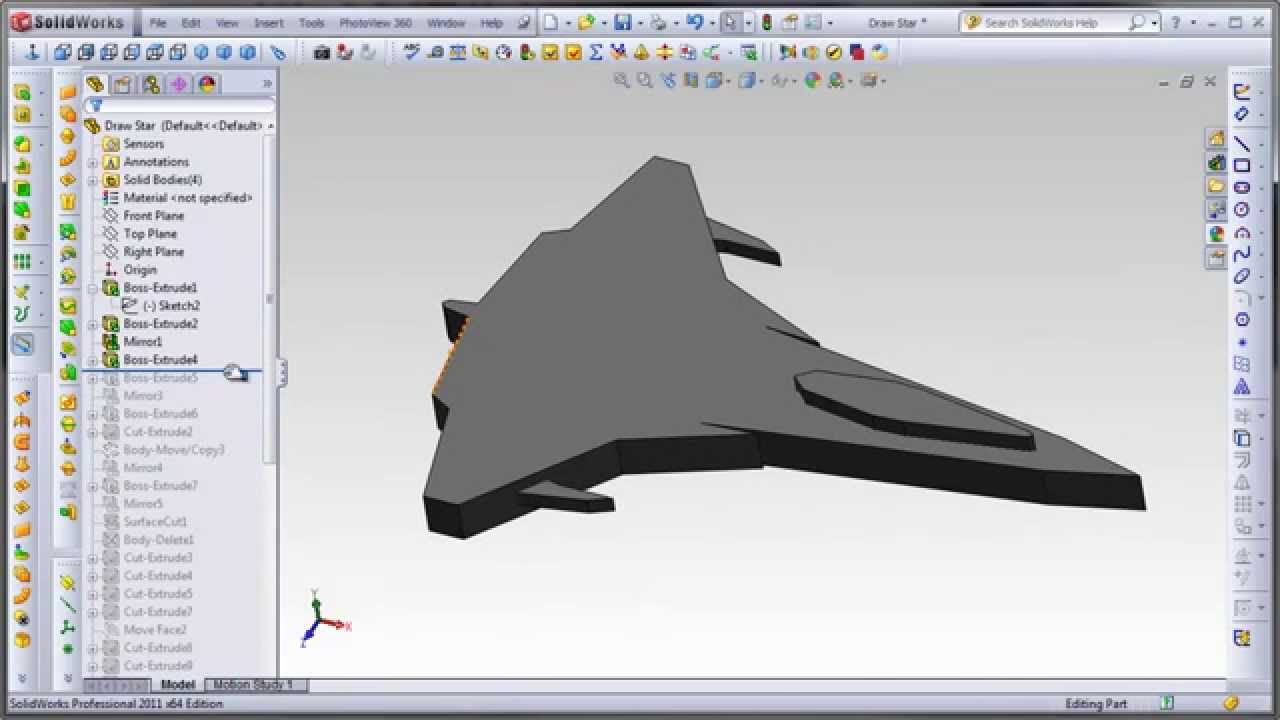
The most accurate method involves modeling the actual fan/impeller blades and solving the study as a sliding mesh (rotating reference frame) problem. There are a few ways to model fans or impellers in SOLIDWORKS Flow Simulation.
